Special Purpose Belt
Sidewall Belts
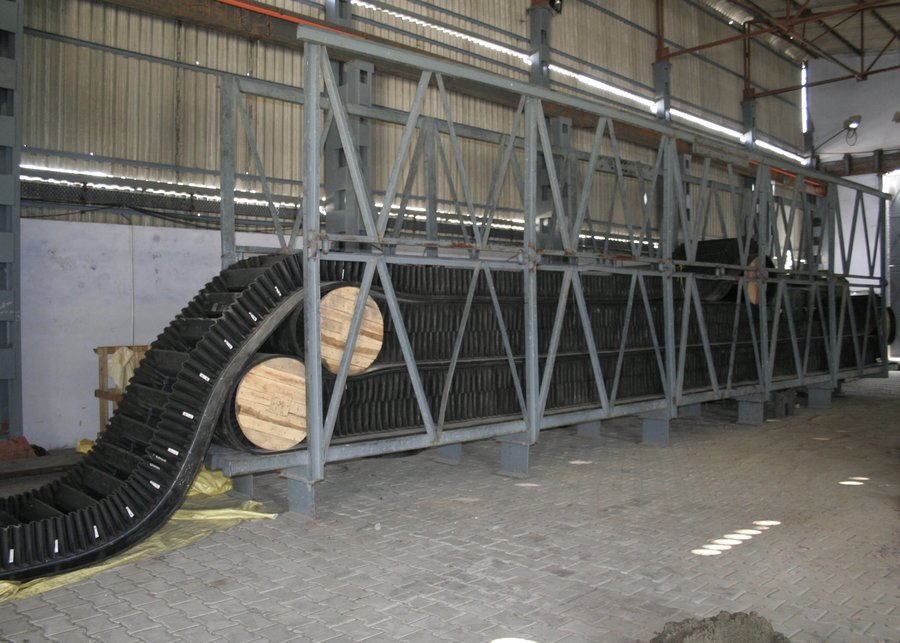
Forech’s unique Sidewall Belts allow end users to carry bulk materials at high inclines and angles up to 90 degrees. This allows material to be carried where space requirements are critical, and increases overall belt efficiency and throughput.
Applications
Forech’s sidewall belts can be used in multiple industries to successfully meet space and efficiency constraints. These industries include:
- Coal and Wood Chips Fired Power Stations
- Underground Mining (coal and ore)
- Ship Loading and Unloading, Ship to Ship loading
- Sand preparation in foundry plants
- Slope conveying in open-pit mining
- Steep angle carrying in road construction machines
Benefits
One of the key advantages of Forech’s sidewall belting is the use of cross-rigid base belts. These specially tailored belts can be deflected from the horizontal to a perpendicular incline and back again without any bowing or sagging in the belt.
This is achieved through custom-made fabric constructions, a special belt composition and our in-house production procedure. This ensures that our sidewall belts have a long life and can withstand operating pressures at high inclines.
Characteristics
Choosing Between Cold and Hot Vulcanised Belts
As sidewall belts usually operate in enclosed conditions, the usual temperature ratings applied to flat rubber conveyor belts cannot be applied. Increased temperature exposure over the life of the belt results in accelerated ageing and a reduction in belt elasticity which adversely effects the belt life.
The effective belt operating temperature therefore determines operating life of the belt.
If the operating temperature is consistently above 70° C, as in the case of heat resistant applications, Forech recommends, use of Hot Vulcanised high angle belts. This is because at high operating temperatures, the cold bonding adhesives used for both the cleats, sidewalls and the belt-splice start to break down. To ensure trouble free service in such applications Forech offers sidewall belts with the cleats and the sidewall in heat resistant quality which are fixed on the base belt with hot vulcanisation.
The operating temperatures listed above for standard quality can be increased by 30°C if a Heat Resistant belt is used.
Downloads
Range
Standard Range of Sidewalls
Sidewall Type | Height | Base Width | Pitch | Weight |
(Swh) | (bw) | (P) | Standard Quality | |
mm | mm | mm | Kg/m | |
N Non Fabric re-inforced | 60 | 50 | 40 | 1.6 |
80 | 50 | 40 | 1.8 | |
100 | 50 | 40 | 2.1 | |
120 | 50 | 40 | 2.3 | |
S Fabric re-inforced | 120 | 50 | 40 | 2.4 |
160 | 78 | 63 | 4.1 | |
200 | 78 | 63 | 5.2 | |
240 | 78 | 63 | 6.2 | |
250 | 75 | 60 | 6.6 | |
280 | 75 | 60 | 7.5 | |
300 | 75 | 60 | 9 | |
400 | 100 | 80 | 18.5 | |
160GB | 75 | 60 | 4.5 | |
200GB | 75 | 60 | 5.5 | |
240GB | 75 | 60 | 6.4 | |
250GB | 75 | 60 | 6.6 | |
280GB | 75 | 60 | 7.5 | |
300GB | 75 | 60 | 9 |
Standard Range of Cleats
Cleat Type | Height | Base Width | Weight |
(Fht) | (bw) | Standard Quality | |
mm | mm | Kg/m | |
T | 40 | 70 | 1 |
50 | 70 | 1.25 | |
60 | 100 | 1.3 | |
C | 70 | 110 | 2.5 |
110 | 110 | 2.9 | |
TCF | 90 | 100 | 2.6 |
110 | 110 | 3.4 | |
140 | 150 | 5 | |
180 | 150 | 5.75 | |
220 | 150 | 7.55 | |
TCF GB | 140 | 150 | 5 |
180 | 150 | 7.35 | |
230 | 150 | 9.75 | |
260 | 160 | 11.9 | |
280 | 173 | 13.9 | |
TCFW | 280 | 270 | 22 |
360 | 270 | 25.5 |
Technology Partner
Steep Angled Sidewall Belts technical partnership.